Net Zero - Real Estate's Challenge
- Alice Devine
- Sep 23, 2021
- 4 min read
Radiant Slabs Rise to the Occasion - and Improve Tenant Experience
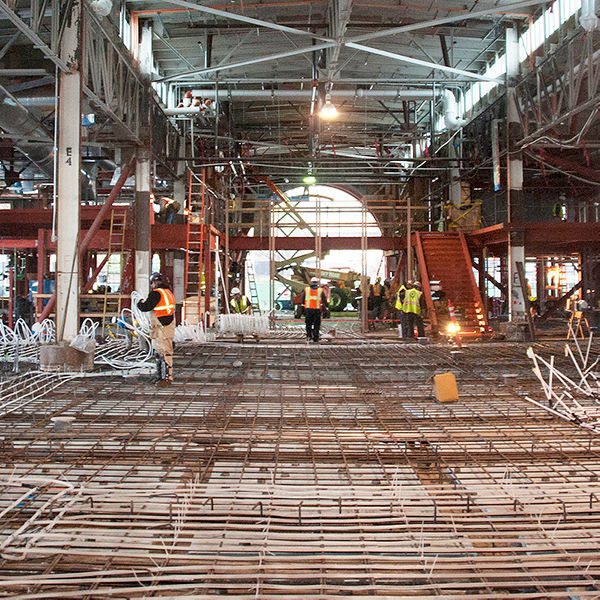
They’re a green alternative to forced-air systems for heating and cooling occupied space.
Silicon Valley’s Fortinet, a cyber security company, and San Francisco’s The Exploratorium museum share a love of science as well as an underground secret: thermal foundations that heat and cool their buildings. These concrete slabs with embedded pipes create a sustainable and comfortable environment.
Modern radiant slabs have shed the copper piping that was popular in the 1970s but was prone to leaks for high-performance, flexible plastic pipes. Moreover, micro-zones create granular, customized temperature regulation for building occupants.
According to the nonprofit Architecture2030, approximately 11% of carbon emissions result from commercial building materials and construction, while another 28% of emissions can be attributed to building operations. Mechanical, electrical and plumbing (MEP) systems account for most of those emissions. By using concrete as a thermal battery, radiant slabs provide a highly efficient means of cooling and heating buildings that reduces carbon and offers a better occupant experience.
Human Biology
Approximately 50% of human heat is garnered through radiance. Noah Zallen, principal and radiant heating and cooling practice lead at the engineering firm Integral Group, draws an analogy to the common experience of climbing into a car on a hot day. Vents may blast air conditioning onto the face, yet the body remains uncomfortably warm because the vehicle’s dashboard and interior still transmit heat.
Translated to real estate, traditional MEP practice focuses on achieving space temperature in the 68- to 74-degree range. Typical offices contain ceiling boxes that blast cool or hot air onto employees, accompanied by noise. Any office occupant knows the all-too-common thermostat wars waged among individuals. Instead, Zallen references a changed mindset that prioritizes cooling (or heating) the body, rather than the space. To that end, radiant slabs heat underfoot or cool overhead with silent fans that work in conjunction with the slab.
Design and Construction
Ancient rammed-earth and adobe structures demonstrate that humans have long relied on building mass to heat or cool structures, as well as to maintain consistent temperature over time. Such construction illustrates a physics principle — the transfer of heat to and from objects.
In radiant slab designs, flexible pipes circulate water or electrical heating elements within the concrete floor, allowing the thermal mass to evenly distribute heat. The economical, cross-linked polyethylene pipe used by Clark Pacific, a California-based firm that specializes in prefabricated construction, uses approximately 20% of the carbon that traditional copper piping requires. As Zallen notes, “in general, carbon is related to the weight of unrecycled metal.”
The lack of metal fan coils and copper piping traditionally seen in MEP systems translates into thinner concrete slabs, less cement and less concrete because of embedded, smaller mechanical systems. For example, Clark Pacific’s prefabricated system eliminates the standard in-the-field topcoat of the concrete slab. The resulting slimmer slabs allow a lower floor-to-floor height without affecting the typical 10-foot interior office ceiling heights. Clark Pacific’s Senior Product Manager Jon Mohle estimates that a six-story standard building can become a seven-story prefabricated radiant slab building without affecting the building envelope or interior ceiling height due to compounded space savings. In turn, more rentable square footage can increase the property’s income stream.
Protecting the Ozone
Radiant slabs protect against refrigerant leaks, an environmental culprit. Traditional VRF (variable refrigerant flow) systems use “extremely large volumes of refrigerant, in highly pressurized bespoke mazes of field-fabricated copper pipe, making refrigerant leakage fundamentally unavoidable,” according to Integral Group’s “Radiant Whole Life Carbon Study.” While any air conditioning system has the potential for such leaks, the integrated, smaller pipes and fewer pipefittings of a radiant system make leaks less likely. In all, Integral Group claims 88% less carbon from refrigerant leakage from a radiant system, even when compared against very conservative industry standard estimates.
Moreover, prefabricated systems have added preventive qualities. By pressurizing fittings in a controlled setting rather than in the field, a factory-assembled refrigerant piping system can lead to rapid flaw detection. Traditionally, MEP engineers hunt for refrigerant leakage when a system registers a drop in pressure or underperforms. But at that point, carbon dioxide has already been released into the atmosphere.
Load Shifting
Timing and demand — particularly for cooling — drives utility expense. Unlike a thermally light building, which must respond to loads when they occur or risk occupant discomfort, the mass in floor slabs provides a buffer.
The University of California, Berkeley’s Center for the Built Environment (CBE) reports that thermally massive radiant cooling systems are often used in pre-cooling mode and turned off during peak cooling periods. This ability to shift electrical demand to off-peak hours and lower pricing allows the building “to do its heating and cooling when it wants to,” says Zallen. Efficiency becomes the reward for the patient accumulation of energy by a thermal mass.
For more fine-tuning, computer scientists at CBE work with algorithms that marry slab control zones to air temperature set points. CBE has conducted simulations for a hybrid HVAC system with under-floor air distribution and a cooled radiant ceiling slab. The energy reduction for a climate similar to Sacramento, California, measured 21%-25% during peak cooling months with superior occupant thermal comfort.
Cost, Savings and Incentives
Clark Pacific’s prefabricated radiant slab system is intended to have cost parity. Mohle acknowledges that “to significantly impact the carbon trajectory of our built environment, low-cost solutions can’t cost more than traditional methods.” In addition, longer-term payoffs of reduced utility bills, energy credits and clean power credits can provide more economic incentives.
Finally, the value-driven decision to reduce carbon can provide a market advantage for securing tenants who share environmental concerns.
Smaller Carbon Footprint
Radiant slabs reduce carbon through combined efficiencies such as using less cement and concrete, lower refrigerant leakage and managed electrical demand. Integral Group’s analysis of precast systems like Clark Pacific's says they offer “conservatively, at least 40% less whole life carbon emissions than a business-as-usual all-electric building.”
And while the prefabricated aspect equates to significant carbon savings, Zallen says that radiant slab buildings, even those constructed in the field, “would still be a positive story.”

Reprinted from my article in NAIOP's Development magazine, Fall 202. Link to the publication: https://www.naiop.org/Research-and-Publications/Magazine
Comments